"Avoid the 98lb Weakling" Structural Tension & Load Bearing
- Lucas Holmgren
- Feb 26, 2024
- 5 min read
Updated: Aug 5, 2024
How to Avoid a 98lb Weakling (In Home Design and Engineering)
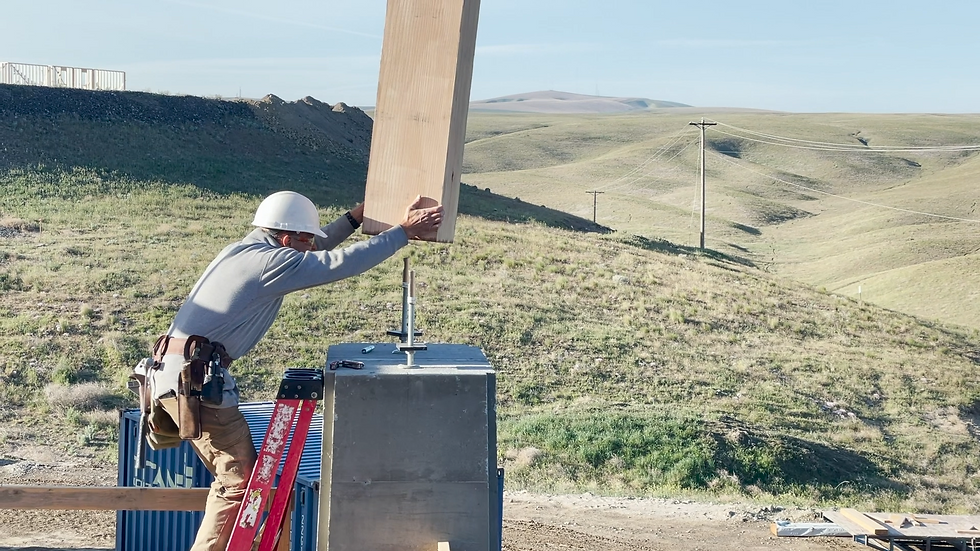
The Number 1 Enemy: Inadequate Planning in Addressing Tension Loads
How will you identify possible weak points in your timber structure?
Is it worth your time?
Can such a complex issue be summarized in an easy-to-grasp format?
If you are mechanically inclined even slightly, I can confidently say:
Yes, it is worth your time.
It is summarized in an easy to grasp format and Yes, you will be able to identify weak points by absorbing the following information and simply applying common sense.
Video Seminar & Article Below
Overview
Part 1 What is a tension load? What role does tension play in the collapse of a structure?
Part 2 Tension loads in a truss .
Part 3 Examples of typical shear systems used to resist tipping over.
Part 4 Tension loads in beam failure and timber grading tips.
Part 1: What is a Tension Load?
A tension load is the force which separates or pulls structural members apart.
This occurs in structural members when they are resisting forces of gravity, wind, or earthquakes. The strength of your timber structure boils down to how well it handles tension loads.
Tension loads tend to be the Achilles heel with most structures, not only in timber framing. A structural member that fails under a compression load blows out on the side has the weakest tension strength.
To understand a timber joint failing under tension, visualize a piece of wood getting pulled apart. Either perpendicular to grain, like a piece of firewood being split, or parallel to grain, like slamming the end grain with a sledge hammer, causing a portion of the timber to slide backwards.
In a home fire, for example, a 2×4 truss will collapse very quickly because it doesn’t take long for the fire to weaken the truss members under tension load. A freestanding pavilion or porte-cochère may blow over in a heavy windstorm if resistances to tension loads are inadequate. A post may buckle or a beam may collapse if wood fibers are unable to bear tension loads.
Part 2: Tension Loads in a Truss
The explanation easiest to grasp comes through in the accompanying videos (above).
In case you’re short on time or can’t view the video here is a short summary: Picture yourself constructing a truss for a building 24 feet wide.
First, you set a 24 foot long 2×4 horizontally across the walls. Next, you install two shorter rafters at an angle on either side to form a peak at the center. You connect the 2×4 intersections at the walls (each end of the 24 foot 2×4.) Gravity holds the peak tightly together as long as the angled 2×4 rafters cannot pull or slide away from the 24 foot 2×4 ends. Now the peak will support a load but the mid-span of all three 2x4s will not.
What to do?
Hang a 2×4 vertically from your solid peak and connect it to your 24 foot horizontal 2×4.
You now have a solid place to post from to support the mid span of both angled 2x4s. After you have installed your angled supports/webs, the roof load travels down through your webs, up through your king post and down through your angled rafters, which is restrained by your 24 foot long 2×4.
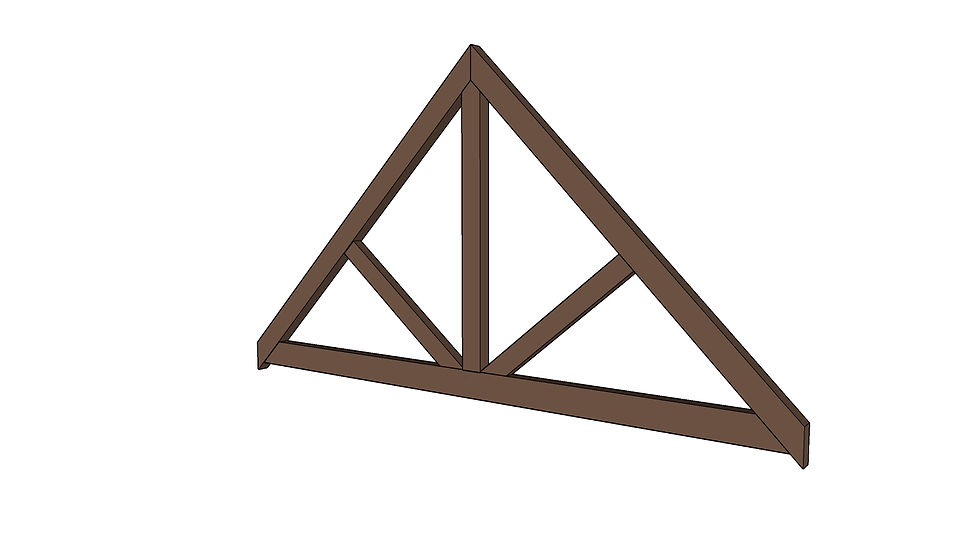
The critical factor is how well your tension loaded joints perform. Timber framers of old were aware of this, which is why you can find many examples of joinery which lock together more tightly as the tension increases. The video also goes through the compression and tension loading of a typical knee brace triangle.
Two favorable factors regarding wind and earthquake loading is:
1. They are not under constant load, as are trusses.
2. The load can be dispersed among many smaller knee braces and joints.
Personally, I like big triangles with angles offset from a 45 degree to take the load more directly, provided that the resulting thrust/tension will be absorbed safely.
Part 3: Lateral Bracing Systems
In timber framing, the key component used to stiffen walls laterally is the age-old knee brace. The simple unassuming triangle. Even a rectangular sheet of plywood under a lateral load has tension from one corner to another, similar to a knee brace.
The following bracing systems are covered in the video and much easier to follow than in a written explanation. You may, however, benefit by reading the unique points listed in the short summary of each system.
Cantilevered System: This is one of the earliest forms of building. Think “pole barn”. Posts buried deeply enough into the ground basically cantilever upwards. Of course, early buildings did not have pressure treated posts, so this method was discarded early on.
Knee Bracing System: Could this be called a reverse cantilevered system? The posts are locked in at the top via tension and compression, and the posts need only to resist breaking under a lateral load. You’ll also want to make sure your post base connection will resist the potential lateral and uplift loading it could face.
Load to Footprint System: Picture 12×12 posts, 4 feet long, standing on end in your garage. How much lateral force will the 12×12 footprint take before tumbling over?
This system basically uses the force and leverage compared to the footprint ratio to calculate how much connection hardware is required to keep the structure from toppling over.
Thru-Tenon System: Not unlike the Load to Footprint System except it works in a horizontal fashion. The “footprint” is the end of the horizontal tie beam where it smacks up against the post. It also has a built-in safety factor, that the tenon itself would have to actually break if the tension peg or pin holding the footprint tight were to fail.
Cruck System: The Cruck System is nothing more than a glorified teepee. Early builders would use crooked trees to gain more head room. Then they got away from the circle but the basic premise remains.
Lean two sticks together and fasten them at the peak. You can find modern day cruck systems in A-framed homes, metal pole buildings, and even churches built with specially made curved glulam beams.
Shear Diaphragm System: Say for example your house is 200 feet long and 30 feet wide. Any lateral load applied to the face of the 200 foot long wall would be transferred to each of the 30 foot long end walls. Force pushes lengthwise at the top of the 30 foot end wall in a horizontal direction.
In other words, the end walls keep it from falling over. What keeps the middle from falling over? You and I know that a 2×4 or 2×6 means nothing for a 200 foot span. All the itty bitty little nails used to fasten the roof plywood all work together in compression and tension to create a rigid shear diaphragm.
In this exaggerated example, a 30 foot wide shear diaphragm would be woefully inadequate. Periodic interior bracing/shear walls definitely would be required. The shear diaphragm is commonly integrated with hybrid timber framing, and even complete timber frames by using floors, walls, and roofs to beef up the structure even more. To achieve a shear diaphragm before plywood was invented, boards were installed at an angle on the floors, walls, or roofs.
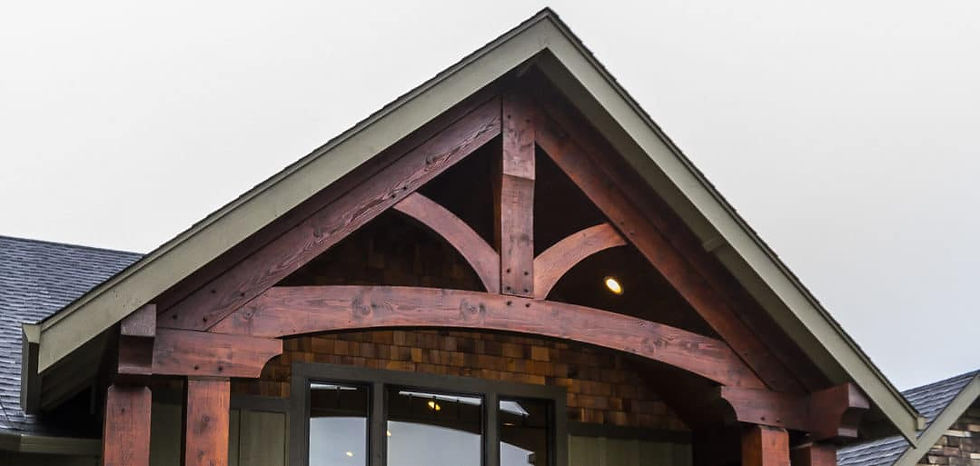
Part 4: Tension Loading in a Timber
The good thing about beam failure is that it happens slowly and it’s very obvious that you’ve got a problem. The wood fibers on the bottom half of the beam are failing under tension load when you have a sagging beam.
Chances are, it just looks ugly but is not an imminent danger because it really takes a lot to snap a beam. But they can snap, so beef up that sagging beam or at least shovel the snow off of your roof before you have a real problem!
To your momentum and success,
Bert Sarkkinen